Posted By Adam Downey on January 18, 2013
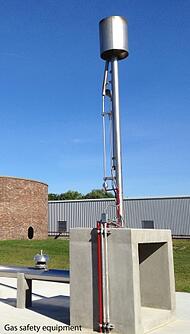
- If anything can go wrong, it will happen at the most inopportune time;
- If there is a possibility of several things going wrong, the one that will cause the most damage will occur first;
- If you perceive that there are four possible ways in which something can go wrong, and circumvent these, then a fifth way, unprepared for, will promptly develop;
- Left to themselves, things tend to go from bad to worse;
- In nature, nothing is ever right. Therefore, if everything is going right, something is wrong;
- If everything seems to be going well, you have obviously overlooked something.
Maybe we can’t avoid falling victim to Murphy’s Law, but there are things that can be done to at least minimize the events we fall victim to. Proper maintenance can reduce catastrophe, but in the bustle of everything else you have to do, it can be all too easy to forget about some of the little things that feed the Murphy’s Law monster:
- Valve and gate exercising: You won’t need to use that bypass line until after the valve or stop gate has become frozen and inoperable.
- Winterizing: This could include disconnecting and draining hoses left outdoors, checking heat tape around exposed pipes, switching the oil out in clarifier drives, and adjusting ventilation rates in buildings to reduce incoming cold air.
- Calibrating and maintaining instrumentation and control equipment: We often rely on alarms and level indicators to tell us things are working normally, but what happens when the alarm horn is broken, the alarm indicator light is burned out, or the pressure transducer fails? Visually verify and calibrate levels and other problem indicators, test control panel indicator light bulbs and alarm horns, and test SCADA communication equipment routinely.
- Gas Safety Equipment: Pop-off valves are supposed to be the last line of defense between an over-pressurized digester lid or aeration line; this means they don’t get used often but are essential when actually needed. What about those atmospheric gas detectors we count on to tell us the chlorine room is toxic or explosive gases have built up in the headworks building? Have they been checked and calibrated lately?
- Electrical Maintenance: I’ll admit, I’m not an electrician; so I don’t want to have to change out a high voltage fuse in the middle of the night. Have your MCC’s and other electrical equipment checked out routinely by a professional.
- Cleaning up: A clean work environment often equates to a safe work environment.
- Everyday cleaning: While you may not want to eat off the floor in your screen building, a clean, dry floor could save you or your fellow employees from a slip and fall, a trip, or other mishap
- Project cleanup: Picking up tools, closing hatches, replacing manhole covers, and checking your project site all need to be done before you leave your work area.
It’s easy to become complacent when things are going well. Take time to review your maintenance program to see if everything is getting done or if things are just being done because “that’s the way we’ve always done them.” It could mean the difference between an inconvenient problem and an utter disaster.
Tags